Securing sustainable growth for the global photovoltaic industry, on a terawatt scale, means considering long-term resource consumption. Silver attracts particular focus. In 2022, 15% of the world's supply will already have been devoted to this industry. Significantly reducing the use of this material is one of the challenges for the future environmental and financial viability of the photovoltaic industry.
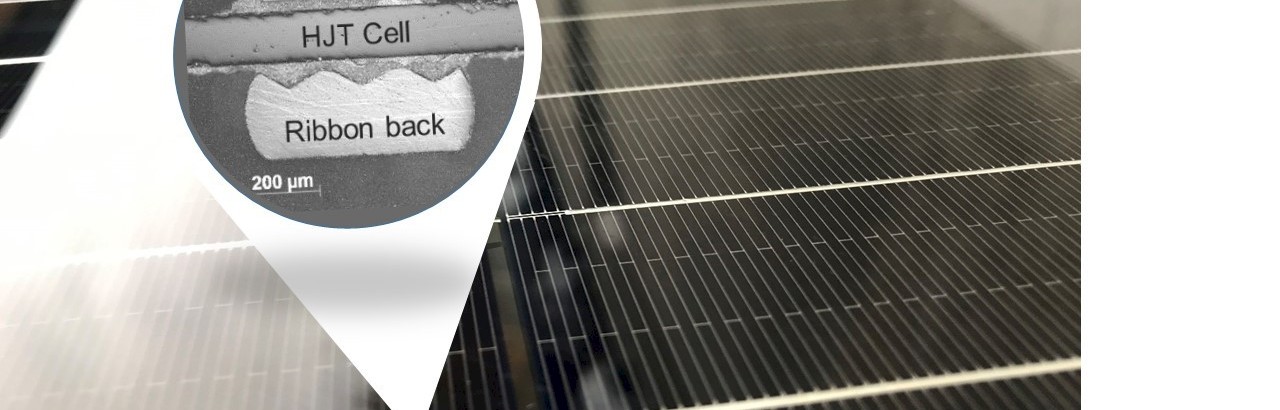
Photovoltaïque plus économe en argent
Silver is used at two stages in the manufacture of photovoltaic cells and panels. It is the conductive ingredient in the screen-printing paste used to print the electrical charge collectors on the surface of silicon cells, the metallization step. It is also present in the materials used to interconnect cells during panel assembly. The aim is therefore to reduce the amount of silver used, or even to replace it at two stages of the manufacturing process.
The silver consumption of bifacial photovoltaic panels using heterojunction technology, including screen-printing and cell interconnection, currently exceeds 35mg/Wp. Experts propose the ambitious target of reducing this figure to 5mg/Wp by 2030. This challenge calls for all means to be employed, such as the co-design of cells and panels, the refinement of printing techniques and the (re)introduction of abundantly available copper.
In addition, the pressure to reduce the use of materials such as Indium and Bismuth is even greater due to their scarcity. This makes the use of low-temperature soldering alloys in their current formulation, which contain these materials, even more unattractive.
The scientific community, and the CEA laboratories at INES, are conducting research in all these areas.
For cell screen-printing, the results obtained by replacing silver pastes with copper-silver pastes are promising. Using this high throughput, industry-standard process, single-sided integration already allows a 33% reduction in silver consumption compared to the pure silver reference, and around 50% for bifacial integration, while maintaining high initial performance. Our tests have also shown that performance degradations of cells and modules produced in this way remain limited to an acceptable range of less than 3% after accelerated aging beyond the industry norm.
For interconnecting heterojunction cells, ribbon gluing technology based on electrically conductive adhesive (ECA) is the preferred choice, particularly as it contains no lead. It's a low-temperature technology that helps reduce residual thermomechanical stresses. Silver reduction in this interconnection technology can be achieved in several ways: reduction in the weight of deposited ECA, reduction of the amount of silver present in the ECA, or reduction/removal of the silver coating on copper ribbons.
By combining the metallization of cells with copper-silver pastes with their interconnection by an ECA with reduced silver content, it will be possible to reduce consumption to less than 20mg/Wp in the short term. Ongoing developments on these subjects suggest that consumption levels of around 10mg/Wp, in line with the international ITRPV roadmaps for 2030, are possible without any significant impact on the power of photovoltaic devices.
Finally, the enhanced performance and lower current density offered by tandem silicon-perovskite devices will undoubtedly provide additional leverage in the future to reduce silver consumption and achieve this objective.
This work was presented at the EU-PVSEC 2023 conference.